Circular connector cable with fieldbus protocol
M Series Circular connector cable and fieldbus protocol: Building blocks for smart industry
In the rapidly evolving field of industrial automation, M-series circular connector cables have become one of the key components for efficient and reliable data transmission.
Circular connectors not only support a variety of fieldbus protocols, but also perform well in a variety of harsh environments with their rugged design and broad adaptability.
What is M Series Circular Connector Cable?
M series circular connector cable is a standardized electrical connection solution, widely used in industrial automation, transportation, medical equipment and other fields. They are named by the diameter of their external threads, such as M5, M8, M12 and M16. M-series connector cables are favored for their compact design, high reliability, and robust protection to meet the needs of everything from signal and data transmission to power transmission.
Basic knowledge of fieldbus protocol
The importance of fieldbus protocols
A Fieldbus is a digital, bidirectional, multipoint communication network for industrial automation that connects field devices such as sensors, actuators, and controllers to a central control system. Compared with traditional analog signal transmission methods, fieldbus has significant advantages:
Real-time: supports high-speed data transmission to ensure the fast response of the control system.
Multi-point communication: allows multiple devices to share the same communication link, reducing cabling costs.
Intelligent: Supports device diagnosis and status monitoring to improve system maintenance efficiency.
Common fieldbus protocols include Profinet, EtherCAT, Ethernet/IP, Modbus TCP, etc. Each protocol has its specific application scenarios and technical characteristics.
Choosing the Right Circular Connector Cable
When faced with a multitude of options, how do you pick the best circular connector cable for your project's needs? Here are a few suggestions that may help:
Define the functional requirements: First of all, it is necessary to know clearly what type of data/signal transmission or power supply the cable will be used for, which will directly determine the selection of the subsequent parameters.
Evaluate the operating environment: Carefully analyze the characteristics of the potential operating environment, such as temperature range, humidity level, presence of corrosive substances, etc., in order to determine whether additional protective measures are required.
Check physical dimensional constraints: Considering the limitations of the installation space, it is sometimes necessary to pay special attention to the overall dimensional requirements of the connector.
Review the electrical parameters: accurately check the maximum voltage and current values required to be supported, as well as other relevant electrical indicators, to ensure that the selected model can fully meet the actual operational requirements.
Confirm interface standards compatibility: Ensure that the selected circular connector complies with established industry standards and allows for seamless interoperability with other components.
Consider long-term reliability: In addition to initial performance, focus on durability and consistency over the life of the product.
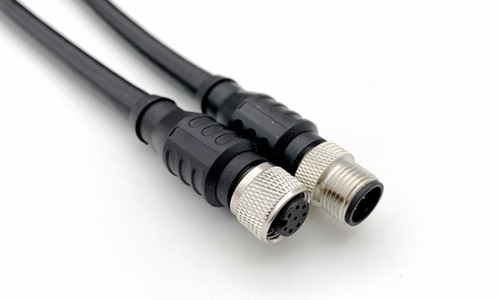
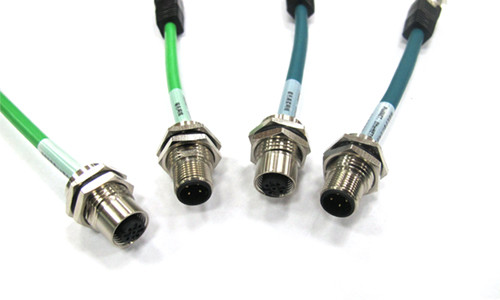
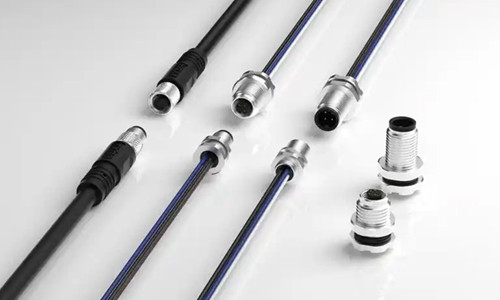
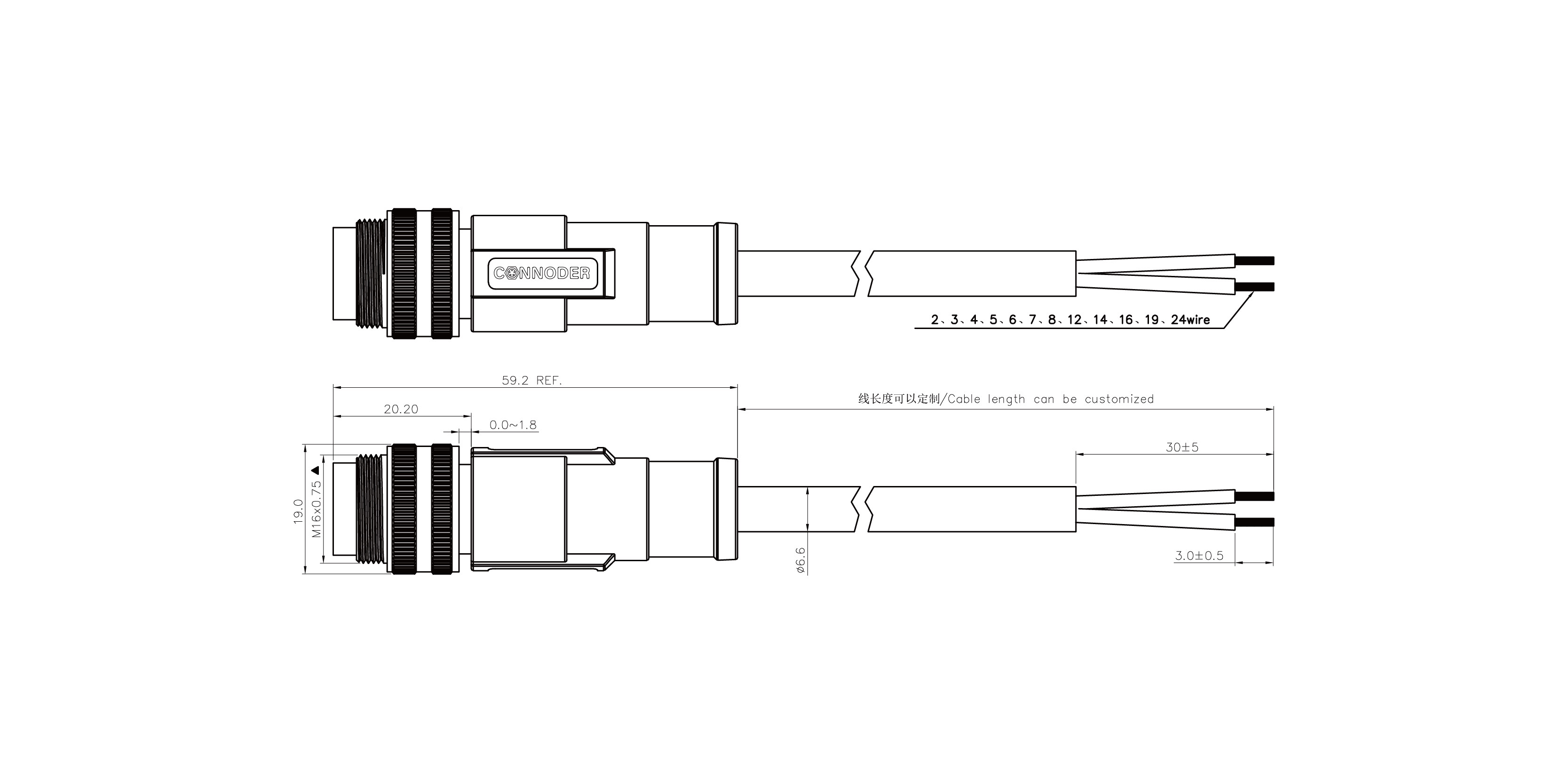