Circular Connector Manufacturing and Production

Manufacturing and Production
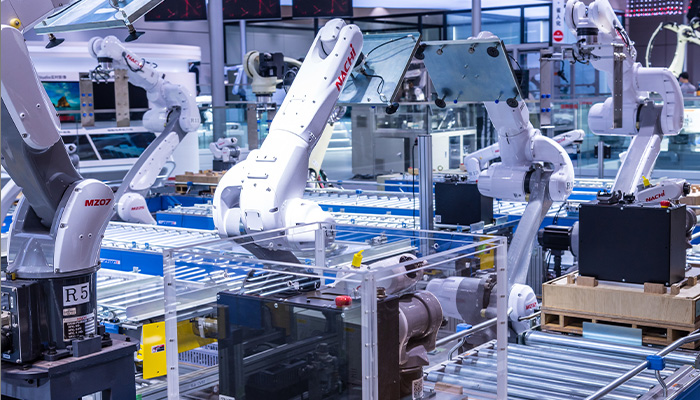
3000㎡
Factory Area
10+
R&D Staff
150+
Country Cooperation
10+
Industry Experience
Circular Connector Innovation and R&D Capabilities

R&D Team
Comprised of engineers and technologists with extensive product development experience, specialising in innovative designs for connectors, cables and accessories.

Technological Innovation
Through continuous technological investment and innovation, we are committed to applying the latest technologies to our products to improve performance and reliability and ensure seamless connectivity between devices.

Innovative Applications
Develop smart connectors to support Internet of Things (IoT) and Industry 4.0 applications, enabling more efficient data transmission and device interconnection.
Circular Connector Production Process
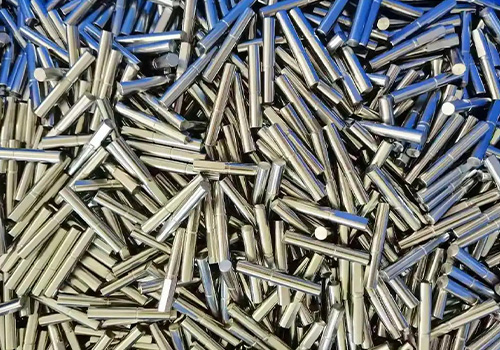
1. Raw Material Preparation
Metal materials: Use high-strength metals, such as aluminum alloy, stainless steel or copper alloy, which have strong corrosion resistance and mechanical strength. The contact point part often uses copper or its alloy, which has good conductivity.
Plastic materials: Such as nylon (PA), polyamide (PBT), etc., which have good electrical insulation properties and high temperature resistance and wear resistance.
Sealing materials: Use waterproof and dustproof sealing rings, using rubber such as silicone, fluororubber, nitrile rubber, etc. or other elastic materials.
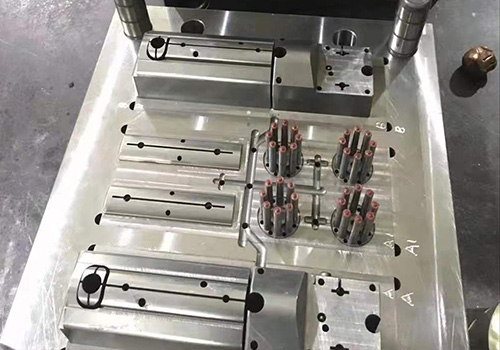
2. Mould Design and Manufacturing
Mold design: Design the corresponding injection mold or die-casting mold according to the specific design requirements of the circular connector, such as size, shape, function, etc.
Mold manufacturing: The mold is manufactured using methods such as CNC (computer numerical control) machine tools or electrical discharge machining (EDM) to ensure the dimensional accuracy and processing surface quality of the mold.
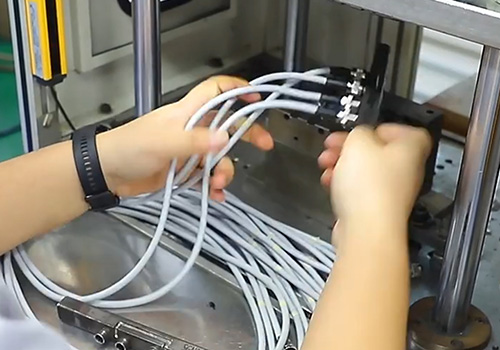
3. Injection Molding/Die Casting
Injection molding: Plastic parts such as the housing and insulator are made using injection molding technology.
Die casting: The metal shell and some internal parts of the connector, such as the contact terminals, are made by die casting.
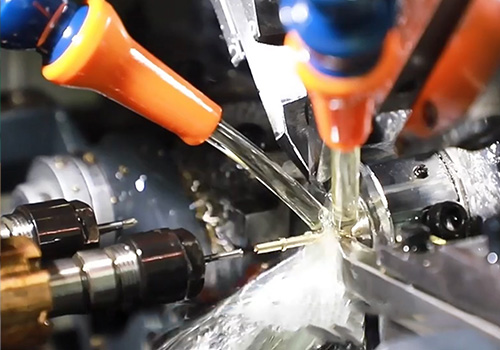
4. Machining and Surface Treatment
Machining: Injection molded and die-cast parts require further machining, such as turning, milling, drilling, threading, etc., to obtain precise dimensions and surface quality.
Surface treatment: Metal parts undergo surface treatments such as electroplating, anodizing, painting, tinning, gold plating, etc. to improve corrosion resistance, enhance appearance, and enhance electrical performance.
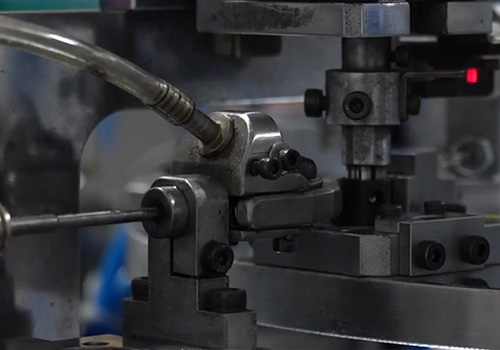
5. Assembly
Pin/contact point installation: The contact points are precisely installed into the insulator of the connector to ensure its stability and good electrical contact performance.
Housing and seal installation: The shell part and the sealing ring are installed in place to ensure the waterproof and dustproof functions of the connector to ensure a good sealing effect.
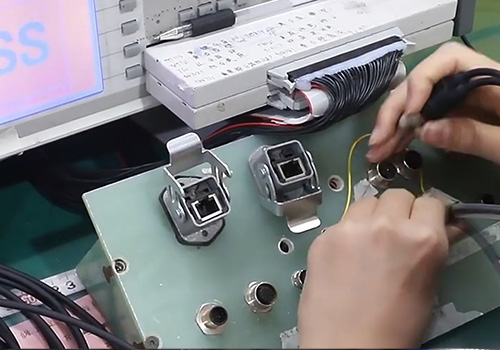
6. Testing
Electrical testing: The resistance of the contact point is within the allowable range and the conductivity is good.
Mechanical testing: Test the mechanical properties such as plug-in and pull-out times, insertion force, and tension to ensure that the product will not become loose or damaged during long-term use.
Environmental testing: Conduct IP rating tests (such as IP67, IP68, etc.) to check stability and reliability under different environmental conditions.
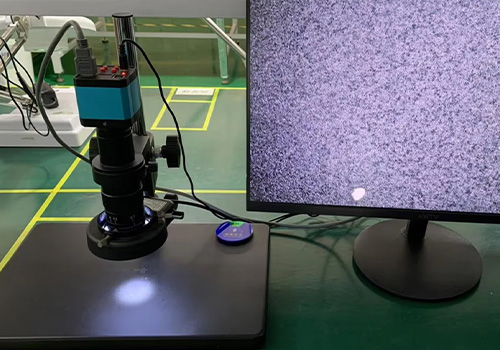
7. Quality Control
Dimensional inspection: Use precision measuring tools, calipers, projectors, coordinate measuring machines, etc. to perform dimensional inspections to ensure that the connectors meet the design requirements.
Functional inspection: Check whether the connection function is normal, ensure the electrical connection, smooth plugging and unplugging, and waterproof and dustproof performance.
Batch inspection: In mass production, batch sampling is used to conduct quality checks on random samples during the production process to ensure overall product quality.
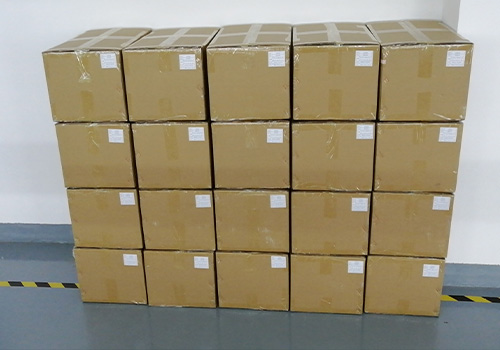
8. Packaging
The connectors are cleaned, labeled, and packaged.
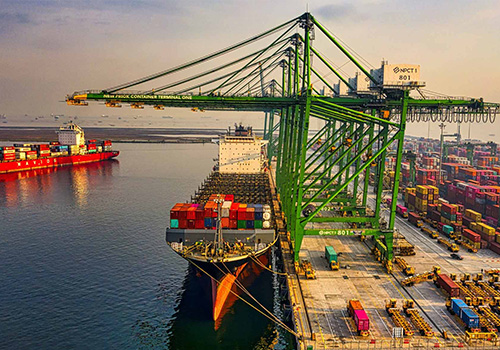
9. Shipping
Once packaged, the connector is ready to ship to customers or distributors.
Circular Connector Production Capabilities
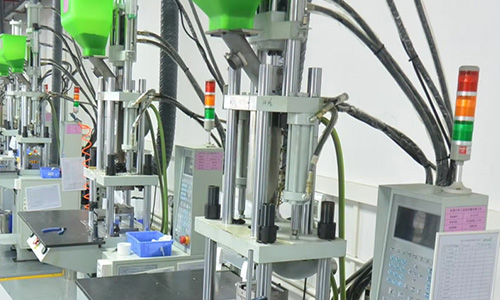
High Precision Injection Molding Machine
Connoder has a professional plastic parts production team, which is specially designed for the production of high-precision, complex-structure circular connectors. It has an advanced injection molding control system that can accurately control temperature, pressure and injection speed to ensure the consistency and high precision of each batch of products.
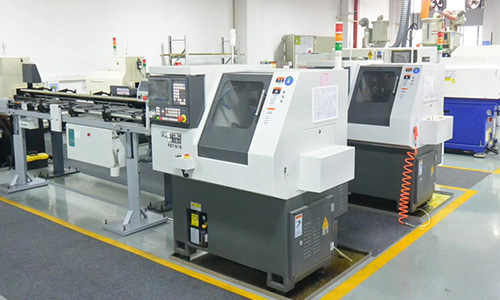
Precision Machining And Production Capabilities
Precision mold design is a key technology in the production of high-precision connectors. In-depth analysis of the functional requirements, material properties, dimensional tolerances and electrical performance of connectors during mold research and development and design ensures that the mold design can accurately replicate complex geometric shapes and tiny details.
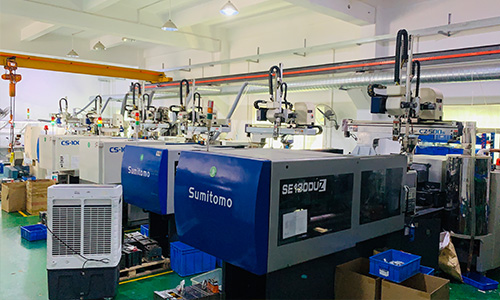
Die Casting
The metal (such as aluminum alloy, zinc alloy) is melted and injected into the mold under high pressure, and then formed after cooling.
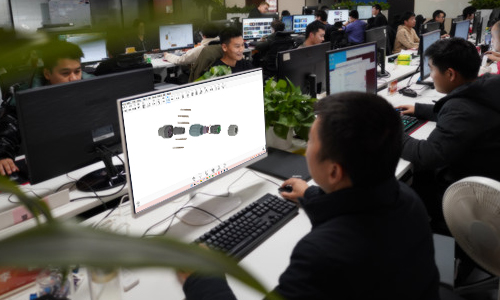
Product Design and Development
Possessing advanced design capabilities, including those that can meet market demand while taking into account production feasibility, the R&D team is composed of engineers and technical experts with extensive experience in product development.
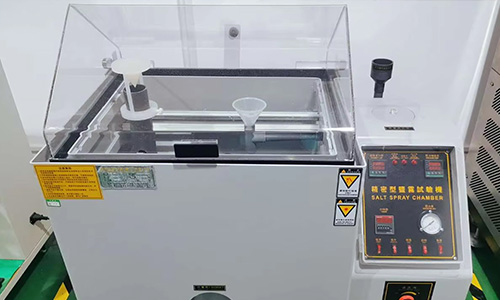
Quality Management and Control
Establish a strict quality management system to ensure high-quality production of products. The production process is fully monitored, and through the implementation of SPC (Statistical Process Control) and other methods, key parameters in the production process are detected in real time to ensure process stability.
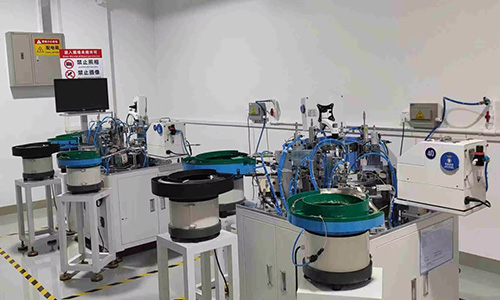
Automated Assembly and Assembly Technology
The production workshop implements automated assembly technology, using industrial robots, vision systems, automated equipment, etc. to perform precise assembly, reduce manual operation errors, and improve production efficiency.
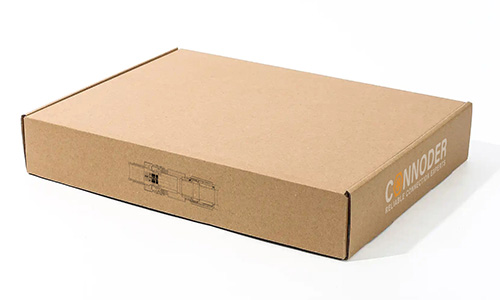
Customizable Brand Logo Printing
We understand the importance of brand identity and can provide a more personalised solution by adding your company logo to the inflator product of your choice.
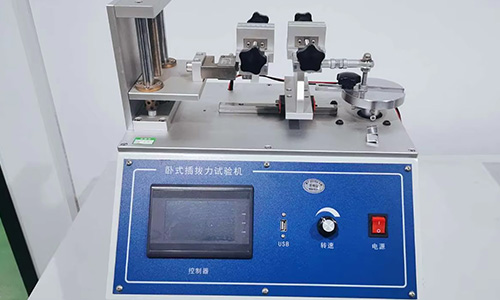
Strict Product Testing
Electrical performance, mechanical durability, environmental adaptability and reliability, etc. By testing contact resistance, withstand voltage, plug-in force, vibration resistance, temperature change, moisture, salt spray, etc., the stability and safety of the connector under different working conditions are ensured.
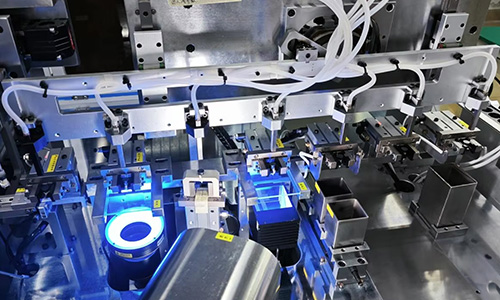
Packaging Workshop
Our team designs suitable packaging solutions based on product characteristics and customer needs. We pay attention to details to ensure that each package meets high standards and effectively protects the product from damage during transportation.
Why Choose Connoder

High-Quality Raw Materials
We have established long-term cooperative relationships with leading global raw material suppliers to ensure that each batch of raw materials meets high quality standards. The use of high-quality raw materials improves the durability and safety of products and provides a solid foundation for production and processing.

Advanced Production Equipment
Equipped with high-precision CNC machine tools, intelligent assembly lines, automated robots and other automated equipment, the production process is efficient, accurate and stable. Quickly respond to market demand, improve production efficiency and reduce production costs.

Professional R&D Team
Composed of engineers and technical experts with rich experience in product development, we focus on the innovative design of connectors, cables and accessories. Through cooperation with leading companies in the industry, we have accumulated valuable practical experience and enhanced our innovation capabilities.

Advanced Testing Equipment
Equipped with advanced testing equipment such as automated testing systems, environmental test chambers and microscopes to ensure the high quality and reliability of products.
Comprehensively used to evaluate electrical performance, material strength and stability in harsh environments, thus providing precise data and high standards of quality control.

Intelligent Monitoring System
Improve production efficiency and product quality through real-time data collection and analysis, monitor equipment status, temperature and humidity, and help production managers quickly identify problems.

Quality Traceability System
By fully recording the data of each production link, the traceability and transparency of product quality are ensured. Using QR code, the system can quickly scan and identify, monitor the production process in real time and generate quality reports.
Connoder's Supply Chain Type
Raw material Suppliers
Provide the plastics, metals and insulation materials required for production.
Accessories Supplier
Provide installation tools, dust caps, sealing rings, etc.
Label and Logo Suppliers
Providing custom labels, logos, compliance markings.
S Supplier
Provide process services such as gluing, gold plating, and spraying.
Packaging Suppliers
Provide packaging materials and custom packaging services.
Logistics Partner
Provide freight, transportation, and logistics distribution services.
Equipment Supplier
Provide CNC machining centers, injection molding machines, and automated assembly systems.
Photography and Visual Display Services
Provide product photography, 3D rendering and visual display services.
Marketing Agencies
Assist marketing agencies to cooperate in market analysis, brand promotion, customer relationship management, etc.
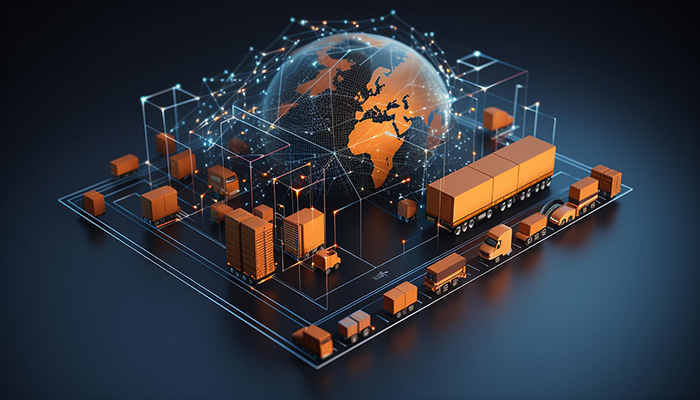
Supply Chain Management at Connoder
Supplier Selection and Evaluation
Based on factors such as product quality, supply capacity, production capacity, delivery timeliness, and price rationality, potential suppliers are comprehensively evaluated, using quantitative and qualitative analysis to ensure that high-quality suppliers that meet factory requirements are selected.
Establish Strategic Partnerships
Establish long-term strategic partnerships with high-quality suppliers, set common quality, delivery and service goals through clear contracts, and enhance the trust and willingness to cooperate between both parties.
Performance Monitoring and Improvement
Regularly use key performance indicators (KPIs) to evaluate supplier performance, monitor product quality, delivery timeliness and response time, and promote improvements in supplier production processes and quality management through continuous feedback.
Risk Management and Response
Identify potential risks in the supply chain, conduct systematic risk assessments, and develop contingency plans to ensure production continuity when market fluctuations or natural disasters occur.
Contract Management and Compliance
Specify quality standards, delivery requirements and responsibilities in contracts, regularly review supplier compliance, ensure that they follow environmental and social responsibility standards, and maintain brand image.
Innovation and Sustainable Development
Encourage cooperation with suppliers to develop new products, promote innovation, and enhance market competitiveness. At the same time, advocate that suppliers use environmentally friendly materials and sustainable practices in the production process to meet corporate social responsibility requirements.
Training and Capacity Building
Regularly train suppliers to improve their technical capabilities and management levels to ensure that they keep pace with corporate development.
Digital Supplier Management
Through the implementation of the supplier management system (SRM), centralized supplier data management, real-time performance monitoring and order status tracking are achieved, and the supply chain process is automated by connecting with the ERP system.
Multi-supplier Strategy and Supplier Integration
Set up multiple suppliers for key components or raw materials to reduce dependence on a single supplier. At the same time, reduce the number of suppliers through supplier integration, optimize management resources, and gain scale advantages.
Please Send Your Message To Us
- Name
- Tel
- *Title
- *Content