Circular Connector Solutions For The Pharmaceutical And Food Industries

Industry Issues

Hygiene And Sterility Requirements
Connectors may become a hidden danger for bacterial growth, and special materials and designs are required to ensure hygiene and meet international standards.

High Temperature And Frequent Cleaning Environment
Equipment needs to be regularly sterilized with high-temperature steam or high-pressure washing, resulting in equipment downtime or increased risk of contamination.

Chemical Corrosion And Humidity Effects
Chemical cleaners or disinfectants are commonly used in food and medical equipment. The corrosion resistance of connectors and high humidity environments may cause oxidation or short circuits inside the connectors.

Frequent Plugging And Unplugging And High Mechanical Loads
Production equipment is frequently disassembled or adjusted, and circular connectors need to cope with high plugging and unplugging times as well as mechanical loads such as vibration and impact.

Electrical And Signal Performance
The accuracy and stability of signal transmission between devices directly affect the efficiency of the production control system.

Compatibility Challenges
There are many types of medical and food processing equipment. Different equipment and interface standards may lead to compatibility issues and increase the complexity of production line design and maintenance.

Installation Restrictions In Small Spaces
Many medical and food equipment needs to be operated in small spaces.

Regulatory Compliance And Traceability
The pharmaceutical and food industries are subject to strict regulations, and connectors need to support traceability systems.
Key Features of Circular Connectors
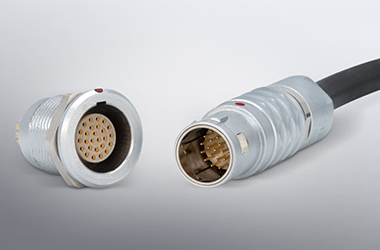
Hygienic Design And Antimicrobial Materials
It adopts a smooth shell design and seamless connection to avoid dirt accumulation and reduce the possibility of bacterial growth.
Uses certified antimicrobial materials that meet the high standards of the pharmaceutical and food industries.
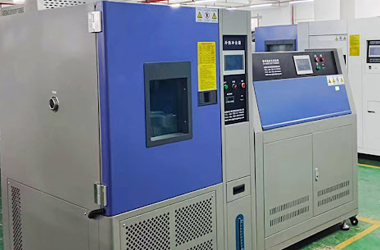
High Protection Level
The Protection Level Reaches Ip69k And Can Withstand High-Pressure And High-Temperature Water Flushing And Corrosive Chemical Disinfectants. Waterproof And Dustproof, It Can Operate Stably In Harsh Environments For A Long Time.
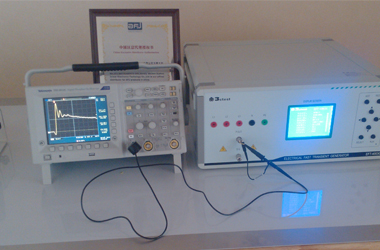
High Mechanical And Electrical Properties
Excellent Seismic And Impact Resistance, High Current Carrying Capacity And Stable Signal Transmission.
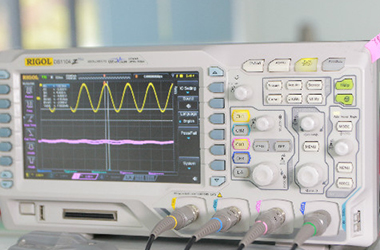
Quick Connection And Easy Maintenance
Quick Plug-In Design Simplifies The Installation And Removal Process And Reduces Equipment Downtime.
The Compact Modular Structure Facilitates Connection Operations In Small Spaces And Improves The Flexibility Of The Equipment.
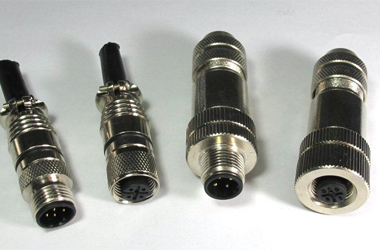
Chemical And Corrosion Resistance
The Shell Material Is Corrosion-Resistant And Can Withstand Long-Term Erosion By Acids, Alkalis And Various Chemical Cleaning Agents.
The Sealed Design Prevents Moisture And Chemicals From Entering The Interior, Extending Connector Life.
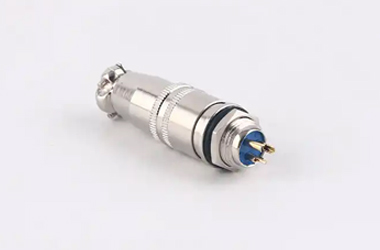
High-Frequency Plug-In And Pull-Out Design
Optimized Mechanical Contact Design Ensures Long-Term Reliability.
The Plugging And Unplugging Life Reaches More Than 5,000 Times, Which Meets The Frequent Plugging And Unplugging Operations Of The Production Line.
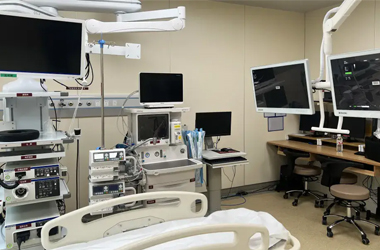
High Signal Integrity
Low Contact Resistance Materials And High Shielding Design Effectively Avoid Signal Interference Or Data Loss.
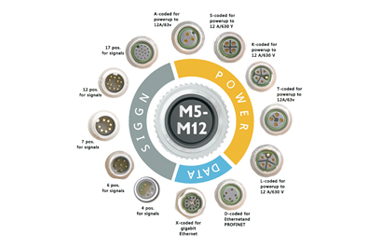
Standardization And Compatibility
Complying With International Standards (Such As M8, M12,M16), It Is Compatible With A Variety Of Device Interfaces And Simplifies Device Selection.
Application Characteristics In The Pharmaceutical And Food Industries
Efficiency and Productivity
It can run continuously and efficiently, ensure stable production speed, is not affected by human factors, and is capable of large-scale production.
Easy To Clean
Equipment and materials must support high-frequency high-pressure and high-temperature cleaning to avoid cross-contamination.
Antibacterial Materials
Use medical-grade or food-grade materials to ensure that the product will not be contaminated by microorganisms during the production process.
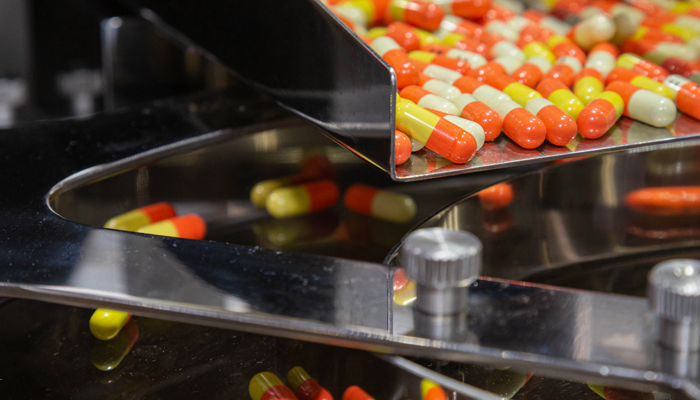
Real-Time Quality Monitoring
The equipment must be integrated with a high-precision detection module that can monitor key parameters in the production process (such as temperature, humidity, flow, etc.).
Consistency
Ensure the quality stability of each batch of products and meet industry regulatory requirements.
Traceability
Record data from each production link (such as raw material sources, process parameters, etc.) to achieve traceability management of the entire process.
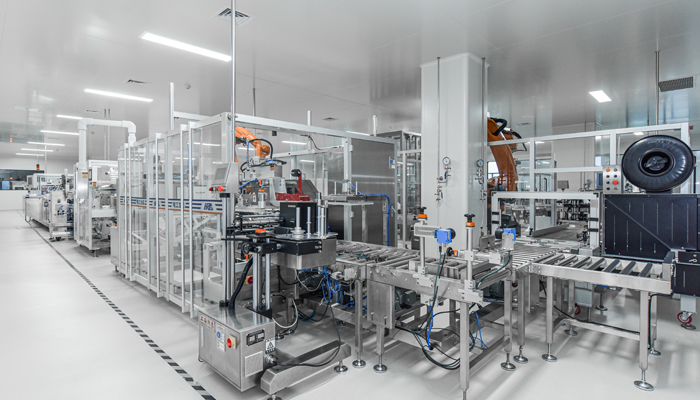
Product Safety
Ensure that each link in the production process does not pose a threat to the safety of the product.
Operational Safety
The equipment must be equipped with a complete safety system (such as emergency stop, protective cover, sensor) to ensure the safety of operators.
Environmental Safety
Use environmentally friendly materials and processes to reduce negative impacts on the environment.
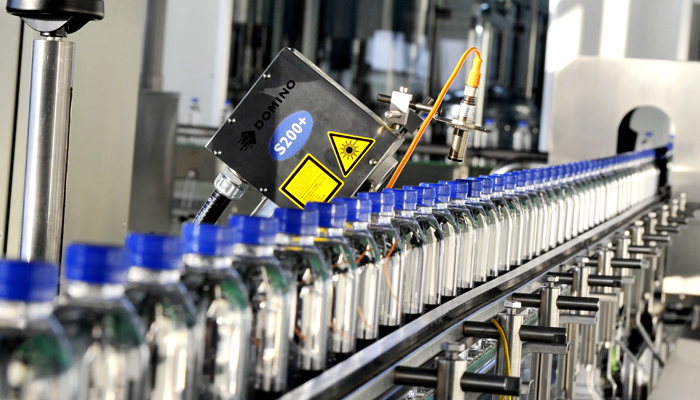
Continuous Operation Capability
The equipment must be able to work continuously around the clock, reduce downtime, and improve production efficiency.
Anti-Interference
Adapt to efficient operation in complex environments, and ensure the stability of signal transmission and equipment control.
Flexible Production
Able to quickly adjust the production process to adapt to the processing needs of different products.
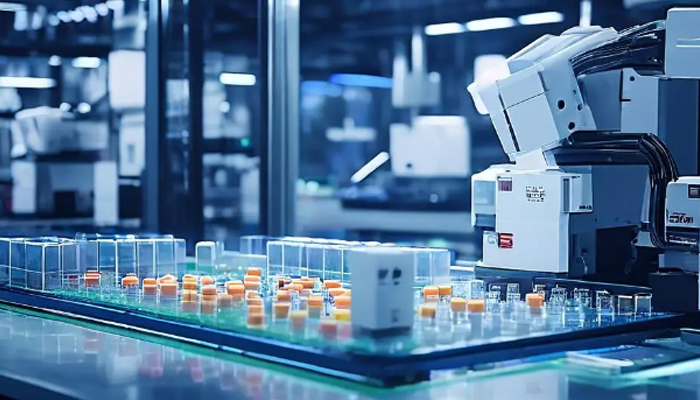
Automated Control
The equipment must be seamlessly integrated with intelligent control systems (such as MES, ERP) to achieve real-time monitoring and optimization of the production process.
Data Collection And Analysis
Real-time production data is collected through sensors and intelligent connectors to provide data support for optimizing processes and improving efficiency.
Artificial Intelligence Application
Use AI technology to predict equipment failures and optimize production scheduling and quality control.
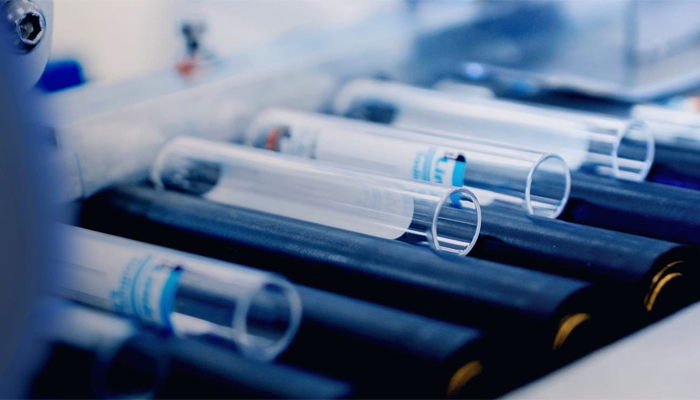
Long-Life Design
Equipment and components must be highly durable to reduce the need for frequent replacement.
Environmental Adaptability
Able to work normally in high temperature, high humidity, low temperature or corrosive environments.
Stable Operation
Performance remains unaffected under high load or harsh conditions to support continuous production.
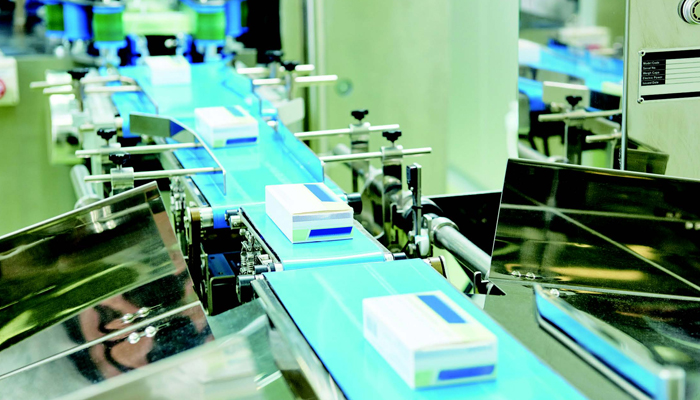
Contact Connoder To Get Your Pharmaceuticals Food Solution
We focus on the R&D and customization of circular connectors.
With 10 years of experience in the connector industry, we are a circular connector manufacturer integrating R&D, production, sales and service. If you have any questions about the automated production line, please contact us and we will provide you with the best solution.
Connection Solutions For Pharmaceuticals Food
Please Send Your Message To Us
- Name
- Tel
- *Title
- *Content