Circular Connectors In Automated Production Lines

Industry Issues

Environmental Adaptability
Some automated production lines work in harsh environments, such as high temperature, humidity, dust, etc.

High Vibration and Shock
Equipment is often subjected to large vibrations and shocks, which affect the reliability of connectors and cause poor contact or disconnection.

Electrical Performance
Electrical equipment on automated production lines often requires high current and power transmission.

Standardization and Compatibility
Automated production lines involve a variety of equipment and systems. There are many types of connectors with different standards, which can easily lead to interconnection problems and increase maintenance difficulty.

Installation and Maintenance
When installing and maintaining connectors, you may encounter complex space constraints, especially inside narrow mechanical equipment, making the connector difficult to install or replace.

Lifespan and Durability
In a high-frequency operating environment, the durability of the connector is particularly critical. Long-term use may cause poor contact or damage, thus affecting the reliability of automated production.

Alternatives to Wireless Connectivity
In some special automated production environments, traditional wired connections may not be applicable, such as mobile mechanical equipment or robots that need to avoid excessive cable interference.

Cost Control
During the production process, using high-quality circular connectors may increase the overall cost of the device, especially in large-scale production.
Key Features of Circular Connectors
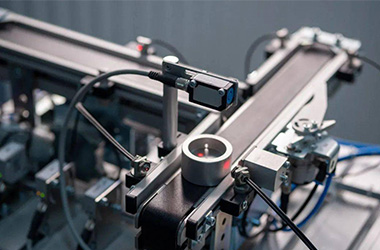
Durability and Long-term Stability
Use high-quality materials such as metals, high-temperature plastics and special alloys that can withstand long-term mechanical operation, vibrations and temperature fluctuations.
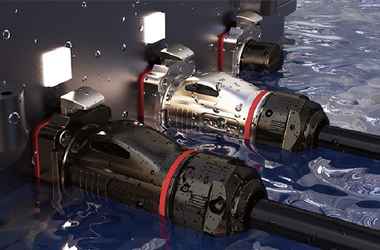
Environmental Resistance
It possesses abilities to resist environmental interference, including being waterproof, dustproof and corrosion-resistant with a protection level of IP67 or above. Also, with the use of corrosion-resistant and high-temperature resistant materials, it can maintain stable electrical connections in chemical corrosion or high-temperature surroundings.
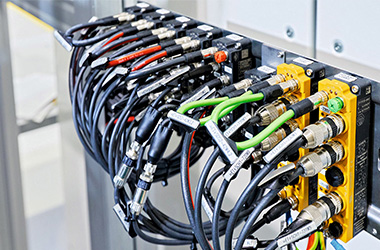
High Current and High Voltage Carrying Capability
It can carry large current and high voltage, and has good contact resistance, conductivity and heat resistance.
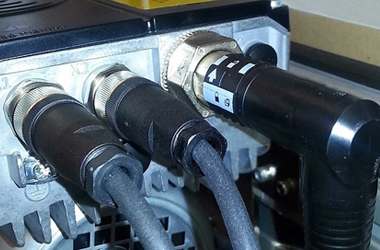
Easy to Install and Maintain
It features easy installation and maintenance with quick connection/disconnection design, reducing operator difficulty and downtime. Its compact and modular design suits limited space and allows easy expansion and upkeep.
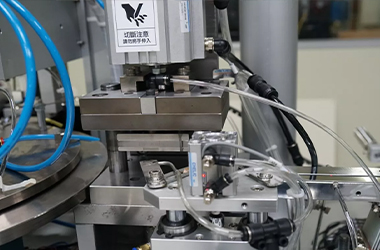
Vibration and Shock Resistance
The spring-type contact design and locking mechanism have strong anti-vibration and anti-shock capabilities, ensuring the stable operation of the equipment.
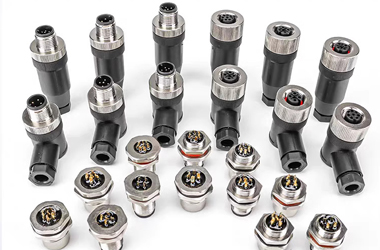
Compatibility and Standardization
It complies with international standards such as M8, M12, M16, etc., and supports multiple interface types and connection methods.
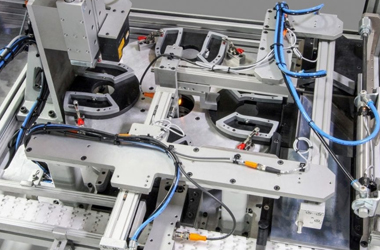
High Signal Transmission Quality
Adopt special materials and structural design to maintain good signal transmission performance.
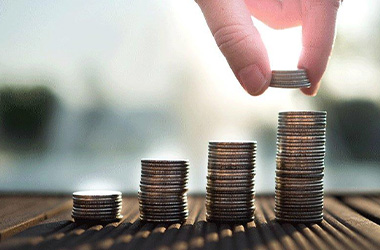
Good Cost-effectiveness
High-quality circular connectors may cost more initially, but their long-term durability and stability mean lower maintenance costs and a longer service life.
Automated Production Lines Have The Following Attributes
Efficiency and Productivity
It can run continuously and efficiently, ensure stable production speed, is not affected by human factors, and is capable of large-scale production.
Accuracy and Consistency
Through precise control systems and sensors, each production link is ensured to be operated accurately and human errors are reduced.
Flexibility and Adaptability
It is highly flexible and can be quickly adjusted and switched according to different product types and production processes.
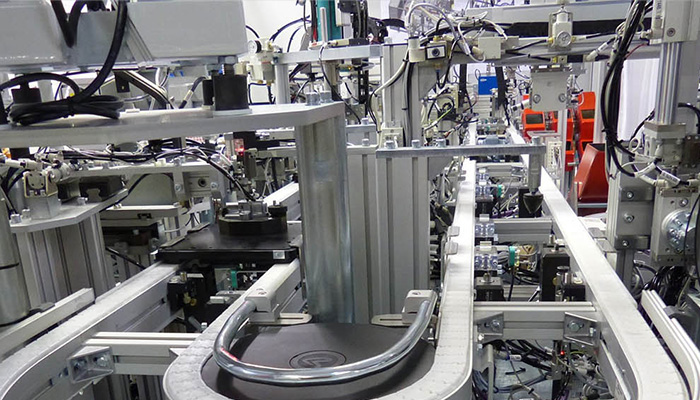
Intelligent Control
Using advanced control systems, such as PLC (Programmable Logic Controller) and DCS (Distributed Control System), intelligent control systems automatically monitor the production process, predict potential problems, perform fault diagnosis, ensure stable operation of the production line, and improve overall production efficiency.
High Security
Automated safety systems (such as emergency stop devices, protective covers, sensors, etc.) are used to ensure the safety of operators, reducing potential safety hazards in manual operations and avoiding equipment damage or personal injury.
Energy Saving and Consumption Reduction
With precise control and efficient operation, automated production lines can effectively reduce energy consumption and material waste, achieve energy conservation and emission reduction effects, and improve the company's green production level.
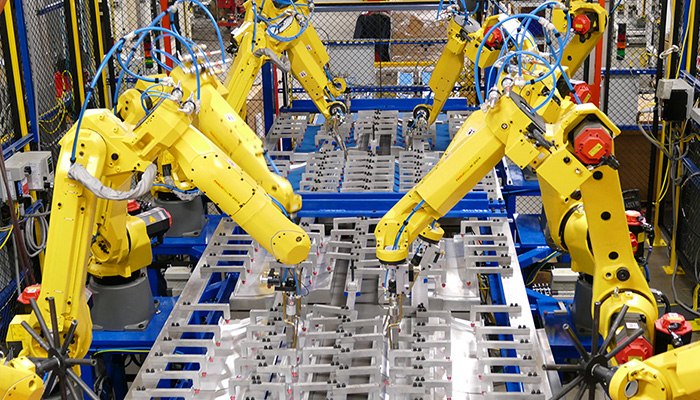
Reduce Manual Intervention
Reduced manual labor intensity, reduced the risk of human error, improved the safety and comfort of the working environment, and reduced dependence on highly skilled labor
High Quality Management
The integrated quality inspection system monitors the quality data of the production process in real time, such as size, weight, color, etc., to ensure high product quality.
Informatization and Data Collection
Equipped with information management systems (such as MES, ERP systems) and data acquisition systems, it can collect and analyze production data in real time to improve overall efficiency.
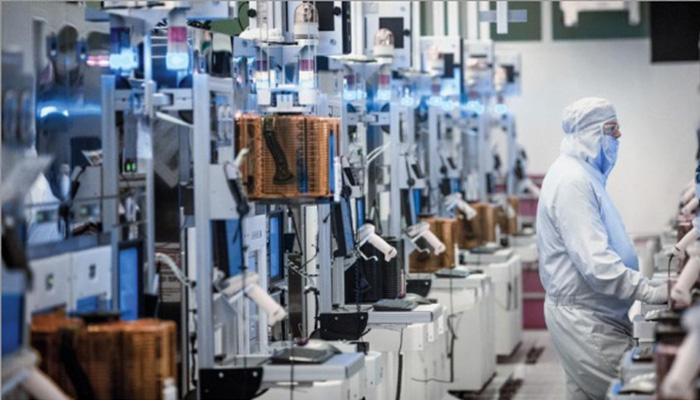
Production Costs
Automated equipment has replaced some dangerous manual operations, reduced production costs, improved production efficiency, and can enhance the market competitiveness of enterprises.
Continuity and Stability
It has high continuity, can work 24 hours a day without interruption, has good equipment stability, reduces downtime, and helps enterprises improve production reliability and long-term stability.
Quality tracking and Traceability
The integrated traceability system can record the production information of each product, including production date, process parameters, raw materials, etc., which helps to deal with and improve problems in a timely manner and improve the level of quality management.
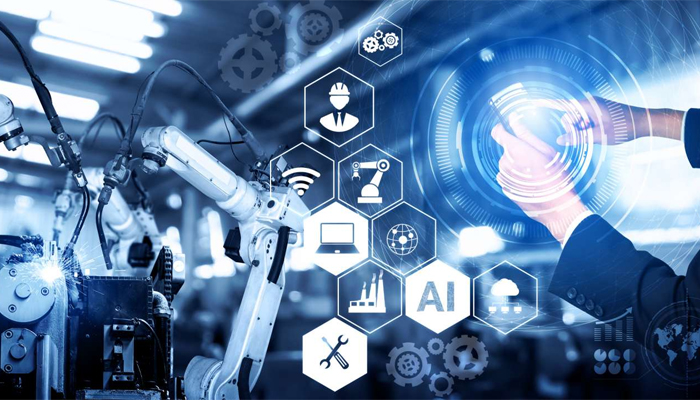
Equipment Interconnection and Remote Monitoring
It has device interconnection and remote monitoring functions, allowing managers to monitor device status at any time through the network.
Standardized and Modular Design
Standardization and modularization are adopted to facilitate expansion, maintenance and upgrading. The configuration can be flexibly adjusted according to the needs, and the subsequent technology upgrade and production expansion can reduce the complexity and cost of production line transformation.
Environmentally Friendly
Optimize production processes, reduce environmental pollution, and effectively treat waste gas, waste water and waste materials generated during the production process.
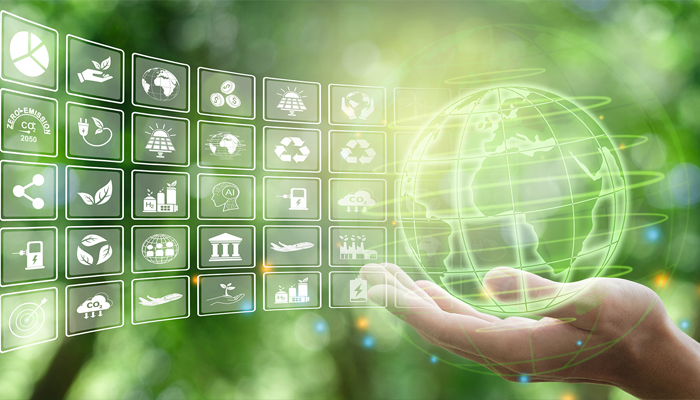
Contact Connoder To Get Your Automated Production Line Solution
We focus on the R&D and customization of circular connectors.
With 10 years of experience in the connector industry, we are a circular connector manufacturer integrating R&D, production, sales and service. If you have any questions about the automated production line, please contact us and we will provide you with the best solution.
Please Send Your Message To Us
- Name
- Tel
- *Title
- *Content