Technical Analysis of Seals
With the development of industrial automation and communication technology, there is an increasing demand for protection of equipment, especially connectors used outdoors or in harsh environments. the M-Series connectors stand out in many application scenarios with their excellent waterproof performance, a feature that is largely attributed to their built-in sealing design.
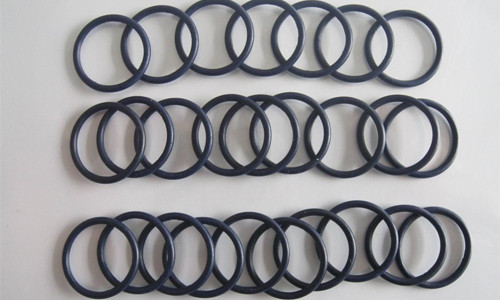
Importance and Mechanism of Seals
The mechanism of action of the Sealing Ring, as an important component inside the connector to prevent the intrusion of moisture and other contaminants, depends mainly on the choice of material and the precise matching of the design.The O-ring is a bidirectional sealing element, which achieves its sealing effect by the initial compression in the radial or axial direction during installation. This extruded seal relies on the elastic deformation of the seal to cause contact pressure on the sealing contact surface, and when the contact pressure is greater than the internal pressure of the medium to be sealed, no leakage will occur.
Selection of Seal Material
Choosing the right seal material is crucial to ensure the waterproof performance of M series connectors. Common sealing ring materials include nitrile rubber (NBR), fluoroelastomer (FKM), silicone rubber (VMQ) and so on.
Each material has its own specific application:
Nitrile rubber (NBR): has good oil resistance and abrasion resistance, and is suitable for sealing needs under general working conditions.
Fluoroelastomer (FKM): excellent chemical stability and high temperature resistance, suitable for sealing in extreme environments.
Silicone rubber (VMQ): with excellent low-temperature elasticity and biocompatibility, it is suitable for the medical and food industries.
According to different application environments, such as temperature, humidity, chemical substances and other factors, the selection of the most appropriate sealing material is to ensure that the connector waterproof performance of the basis.
Design and Manufacturing of Seals
In addition to the choice of materials, the design of the seal is also one of the key factors in determining its performance. Reasonable cross-section diameter, compression rate and stretching amount are essential to ensure the sealing effect. For static sealing applications, a compression rate of 15% to 30% is usually recommended, while for dynamic sealing applications it is 10% to 15%. Seal ring dimensional accuracy and surface quality directly affects the sealing effect after assembly, in the production process need to strictly control the tolerance range, and the use of precision molds for processing.
Application examples of seals in M series connectors
The waterproof function of the M12 connector, for example, depends mainly on the built-in waterproof seal. In order to achieve IP67 or even higher levels of protection, in addition to the selection of high-performance sealing materials, it is also necessary to consider the fit between the seal and the connector housing. In some designs, special sealing structures, such as double-layer seals or multi-point contact sealing methods, are used to further enhance the waterproof effect.
For different types of M series connectors, the design of the seal will also vary to better suit the specific installation conditions and use scenarios.
Testing and verificatio
In order to ensure that the seal can meet the expected waterproof requirements, it must be rigorously tested and verified. Commonly used testing methods include hydrotesting, immersion testing, etc. These tests not only assess the waterproof performance of seals under static conditions, but also simulate various situations that may occur under actual working conditions, such as vibration, impact, etc., so as to comprehensively check the reliability of the product.
Seal technology is at the heart of improving the waterproof performance of M-Series connectors. Through careful selection of sealing materials, optimization of design parameters and strict implementation of the production process, the waterproof capability of the connector can be significantly improved. For Connoder, continuous focus on the R&D progress of new materials and technological innovation, as well as continuous improvement of existing products, will be the key to remain competitive. In the future, the requirements for waterproofing of connectors will only become more stringent, which will push sealing ring technology to a higher level.
Please note that the “M series connectors” mentioned in the above article specifically refer to industrial standard connectors such as M8 and M12, which are widely used in sensors, actuators, encoders and other equipment, especially in environments that require high levels of protection. The success of these connectors is supported by high-performance seals.